Metal FFF 3D Printing Services
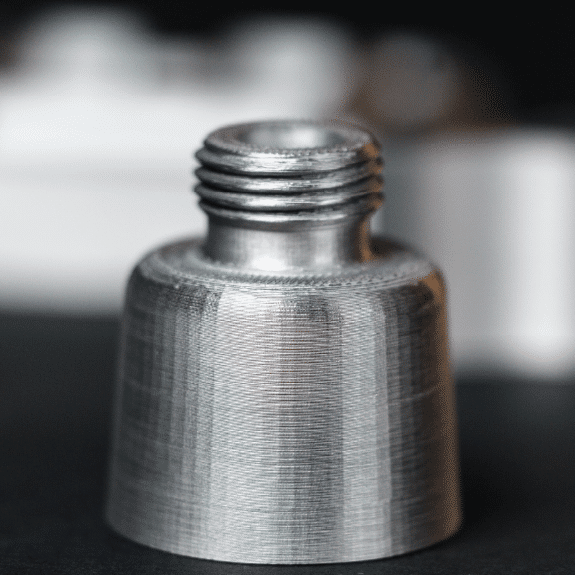
Low Cost Without Compromising Quality
Discover the groundbreaking 3D printing method for custom, durable metal parts
Thanks to Markforged Metal X 3D printing technology, affordable and powerful metal printing is now easily accessible.
From stainless steels to copper, there is a wide range of materials to choose from when it comes to creating consistent, quality parts.
How Metal FFF 3D Printing Works
After uploading your part design as an STL file, the printer software determines where support material is needed for a successful print. It then sends the job to the printer where parts are printed layer by layer, with metal powder bound in plastic.
Once the print job is complete, parts are put into a wash system to dissolve the plastic binding matrix around the metal powder. Then, parts are put into a furnace to fuse the metal powder together into a solid, ready to use part.
Explore Popular Uses for Metal FFF 3D Printing
- Metal prototypes
- Brackets and fixtures
- End-of-arm tooling gripper jaws
- Air intake manifolds
- Actuator housings
Technical Specifications
|
Metal FFF 3D Printing
|
---|---|
Lead Times
|
Standard lead time is 5 days (expedited option available).
|
Standard Build Layer Thickness
|
50-125 microns (depending on material selection).
|
Build Envelope
|
300x220x180mm (XYZ).
|
Available Materials
|
17-4 PH Stainless Steel, A2 Tool Steel, D2 Tool Steel, H13 Tool Steel, Inconel 625, Copper
|
Minimum wall thickness
|
0.040″ is commonly accepted (dependent on material and nozzle size).
|
Minimum feature size
|
0.020″ (dependent on layer height).
|
Minimum hole diameter
|
0.060″ for X/Y axis; 0.040″ for Z axis.
|
Minimum Unsupported Overhang Angle
|
45 degrees.
|
Frequently Asked Questions
STEP or STL file.
A3D Manufacturing is staffed with materials science engineers to help you in determining which material needs you might have for your application.
We can help you select the best material for your use case.
Every metal FFF part gets reviewed by an application engineer during the quoting phase to ensure the part is a good fit for this process.
If there are any modifications that will need to be made for the process to work, our team will notify you and help with optimizing your design for 3D printing.
Price is directly correlated to material consumption, printer build time, wash time, and the number of sintering runs needed.
Self-supporting angles help to reduce support structures. In-fill selection and layer height also strongly influence both parameters.
Yes, post machining parts is possible.
If you have machining requirements that need to be considered after printing, please let us know so we can set up your build accordingly.
The metal that is printed is ~96% dense solid metal.
But just like other FFF/FDM technologies the interior structure may have sparse fill (different in-fill types exist including solid fill) depending on part geometry.